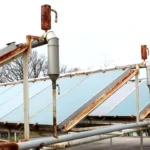
Corrosivity Class C5: Guide to Severe Corrosion
14/10/2024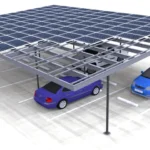
Driving Sustainability in UAE The Rise of Solar Carports and EV Charging Stations
30/12/2024Understanding C1 to C5 Corrosion Classifications
Corrosion poses a significant threat to the durability of metal structures, especially in industrial and marine environments. When steel and aluminum are exposed to various atmospheric conditions, corrosion resistance becomes essential to extend the lifespan of these materials. The C1 to C5 corrosion classifications, as defined by international standards like ISO 9223:2012, provide a comprehensive framework to categorize different corrosive environments and suggest appropriate protective treatments. In this blog, we’ll explain each corrosion class and offer tips for maximizing metal protection.
What Are the C1 to C5 Corrosion Classes?
The C1 to C5 corrosion ratings classify environments based on their corrosivity, from C1 (very low) to C5 (very high). Understanding these classes can help you determine the best anti-corrosion strategies for your metal structures.
Here’s a breakdown of each classification:
1. C1 Corrosion Class (Very Low Corrosivity)
Typical Environment: Heated indoor spaces with clean air, such as offices or residential buildings. Corrosion risk is minimal in these environments.
Recommended Protection: Aluminum typically requires a chrome-free surface conversion. For steel, a simple degrease or shot blast may suffice.
2. C2 Corrosion Class (Low Corrosivity)
Typical Environment: Unheated buildings where condensation may occur, like warehouses or sports facilities.
Recommended Protection: Aluminum should have a 40µ chrome-free coating, while steel may need a zinc primer or galvanizing for enhanced corrosion resistance.
3. C3 Corrosion Class (Medium Corrosivity)
Typical Environment: Areas with moderate humidity and some air pollution, such as cities and industrial zones.
Recommended Protection: Apply a thicker coating (60µ or more) for aluminum. Steel should undergo shot blasting followed by priming to provide adequate protection against corrosion.
4. C4 Corrosion Class (High Corrosivity)
Typical Environment: Chemical plants, swimming pools, and coastal areas where salt and moisture are prevalent.
Recommended Protection: For aluminum, an 80µ chrome-free coating is advised. Steel structures require galvanization and zinc primers to withstand high-corrosivity environments.
5. C5 Corrosion Class (Very High Corrosivity)
Subdivided into C5-I (Industrial) and C5-M (Marine)
Typical Environment: Harsh industrial zones with continuous moisture exposure or marine environments with salt spray.
Recommended Protection: Heavy-duty coatings (140µ-160µ) and specialized waterproof primers are crucial. Aluminum may need a chrome-free surface conversion with a waterproof primer, while galvanized steel should also be treated with a waterproof primer for maximum corrosion resistance.
Essential Tips for Corrosion Protection
To achieve optimal corrosion protection for metal structures, consider the following best practices:
Pre-treatment Procedures: Utilize acid etching and chrome-free conversion processes like Titanium Zirconium for aluminum and Silane technology for galvanized steel.
Regular Maintenance: Follow the manufacturer's maintenance recommendations to preserve the integrity of the coatings and prolong the lifespan of the structure.
Adequate Coating Thickness: Ensure that the coating thickness matches the specified requirements, such as 140µ for high-corrosivity environments, to offer effective protection.
Why Corrosion Classification Matters in Metal Fabrication
Understanding C1 to C5 corrosion classifications is essential for engineers and fabricators who design metal structures exposed to different environmental conditions. By adhering to the appropriate corrosion class guidelines, you can significantly enhance the durability of steel and aluminum components, reduce maintenance costs, and ensure compliance with safety standards.
for expert solutions tailored to C1 to C5 environments.
Get in touch now to ensure lasting protection!